Через тернии к золоту
За всю историю человечества было добыто около 170 тысяч тонн золота. Основная его часть осела в подземных хранилищах банков в виде слитков, некоторое количество — на пальцах, в ушах и на шеях, что-то покоится в сундуках на дне морей, а что-то летает в космос и находится в наших карманах в виде частиц микроэлектроники в мобильных телефонах.
Большую часть из этих 170 тысяч тонн получили за последние 150 лет. Сегодняшние масштабы отрасли свели бы с ума золотоискателя XIX века: в год в мире добывают 3 тысячи тонн золотых слитков, а для их размещения нужно 100 железнодорожных вагонов! И немалую часть этого золота добывают у нас, в России.
Месторождение — обогащение — выплавка. Именно такой нехитрый, на первый взгляд, путь проходит крупинка золота, чтобы попасть из недр земли в ваше обручальное кольцо или в слиток в хранилище банка. Путь нехитрый, но довольно тернистый, как вы могли видеть по репортажам с карьера и обогатительной фабрики. Золото остается только выплавить — казалось бы, что проще? Но все не так легко, как кажется! Вы же помните, что в золото превращают камень, поэтому даже на финальном этапе нужно потрудиться.
Отправляемся на Амурский гидрометаллургический комбинат компании Polymetal — сюда привозят золоторудный концентрат с обогатительной фабрики Албазино в Хабаровском крае и с Майского на Чукотке.
На комбинат за год поступает около 160 тысяч тонн концентрата, который в бигбегах зимой везут на грузовиках по зимнику, а в теплое время — на баржах по Амуру. Для извлечения золота из той руды, которая приходит на Амурский комбинат, используется метод автоклавного окисления. По сравнению с другими методами, у него выше степень извлечения, что в случае с золотом крайне важно.
Гидрометаллургический комбинат начинается со склада сырья — как и обогатительная фабрика. Но если на фабрике это были горы камня с разной степенью содержания драгоценного металла, то здесь ровные ряды 16-тонных «авосек» с флотоконцентратом — золотосодержащими серыми шариками. В каждом из таких бигбегов около 700 граммов золота.
Первым делом бигбеги с концентратом выгружаются в измельчитель, или, как здесь говорят, растариваются. Измельчитель как две капли воды похож на ту мельницу, которой перемалывают камни на обогатительной фабрике, только гораздо больше. Шары диаметром 60-100 миллиметров снова превращают концентрат в муку, к нему добавляется вода, и затем насосы перекачивают пульпу в накопитель.
Интересно, что пульпа с разных месторождений (майского и албазинского) поступает в разные накопители, потому что в них отличается содержание серы. Для наилучшего результата реакции окисления важно конкретное содержание серы, и это достигается при помощи коктейля из этих двух накопителей. Коктейль готовят в специальной емкости объемом 500 кубометров. Конечно, за это отвечает не бармен с шейкером, а система автоматизации.
Когда смесь готова, ее отправляют в автоклав — главный агрегат на комбинате. Этот огромный девайс для комбината изготовили по специальному заказу в Азии и доставили сначала морем во Владивосток, а затем на специальных железнодорожных платформах на место строительства комбината в 2011 году. Это была целая спецоперация: вес автоклава — 163 тонны, а длина — 25 метров. Лишь когда автоклав был установлен, приступили к монтажу остального оборудования и постройке корпусов. Так что можно сказать, что все предприятие строилось вокруг этого автоклава.
Так как флотоконцентрат получен из упорных руд, частицы золота в нем заключены в микроскопическую оболочку, и для извлечения золота ее нужно разрушить. Это и происходит в автоклаве методом окисления. Именно поэтому — чтобы обеспечить химическую реакцию — в пульпе и должно быть определенное количество серы. Реакция происходит примерно при 200 градусах под давлением в 21 атмосферу.
Внутри автоклав разделен на пять секций разного объема, снабженных агитаторами, через которые внутрь под каждый агитатор подается кислород. Кислород вырабатывается на специальной кислородной станции здесь же, на комбинате. Во время работы автоклава достигается окисление серы до 98%. Далее окисленная пульпа охлаждается до 40 градусов и отправляется на нейтрализацию.
При нейтрализации используют суспензию известняка и извести. Далее пульпу отправляют на сорбционное выщелачивание в специальных емкостях, при котором используется активированный уголь и цианид натрия. Сначала подается цианид. Он переводит обычные частицы в заряженные ионы. Затем эти ионы осаждаются на активированный уголь, который движется навстречу золоту. Сорбционные емкости установлены каскадом так, чтобы начало сорбции было выше ее конечной стадии. Из емкостей пульпа перетоком стекает в конец процесса. В результате получают уголь, на который собрано все золото из пульпы. Теперь это жидкое золото. Волшебство!
Все эти процессы протекают беспрерывно и под автоматическим контролем из центра управления.
Но жидкое золото никому не нужно, поэтому необходимо перевести его в твердую форму. Делается это при помощи электролиза. Десорбирующий раствор золота отправляют в электролизер. В нем на катоды и аноды подается рабочий ток. В процессе электролиза золото осаждается на катоде. Ну а далее катодный осадок отправляют на финальную стадию — в строго охраняемую комнату по выплавке золота. Здесь сушат катодный осадок в печах и шихтуют его с помощью соды, буры и селитры, чтобы вывести из металла остающиеся примеси.
Получившийся в результате серый порошок отправляют в плавильную печь.
Температура плавления золота — 1064 градуса. Когда золото, что называется, закипело, его варят еще около часа. Так и говорят: «Нужно, чтобы металл проварился». Разлив начинают при температуре около 1200 градусов, и увидеть это может мало кто — настолько строгие меры безопасности на участке плавки золота.
Содержание золота в этих слитках разное, и это не 99,99%, как думают многие. В начале разлива металл легче, в нем меньше проба, к концу проба выше. После того как слитки остынут и с них удалят шлак, с каждого снимается проба.
Это совсем не то золото, которое хранится в банках, — это так называемый сплав доре, и содержание золота в нем около 70%. Банковские же слитки и золото высшей, 999,9 пробы производят из слитков доре на аффинажных заводах. В других же условиях получить золото из слитков доре невозможно.
Поэтому, когда из самолета одной канадской компании в Якутии выпали слитки, у охотников за легкой добычей не было особого смысла их искать. Эти слитки просто невозможно ни кустарно переработать самим, ни продать ювелирам: они им не нужны даже бесплатно.
Вот так крупинке золота приходится пройти тернистый путь — из каменных глыб на дне карьера до золотых слитков. За ним стоит труд огромного количества людей и десятки технологических операций.
А вы знали, что у нас есть Telegram?
Подписывайтесь, если вы ценитель красивых фото и интересных историй!
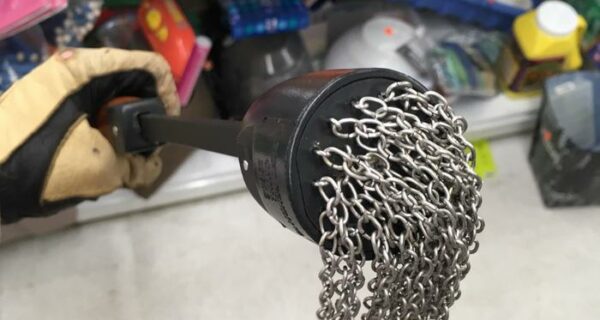
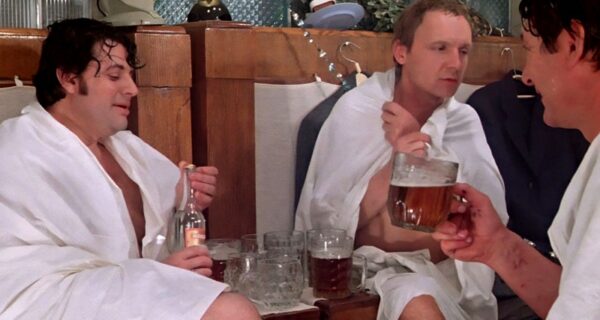
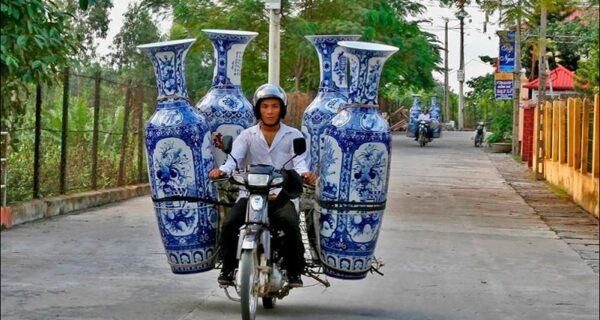
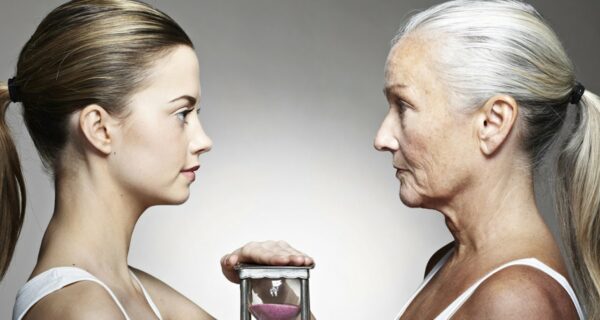
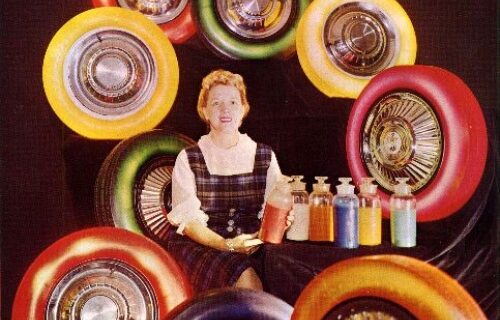
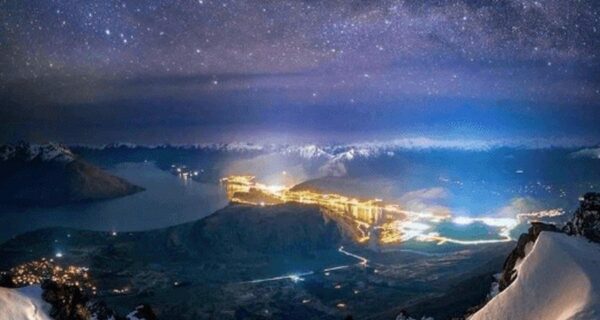
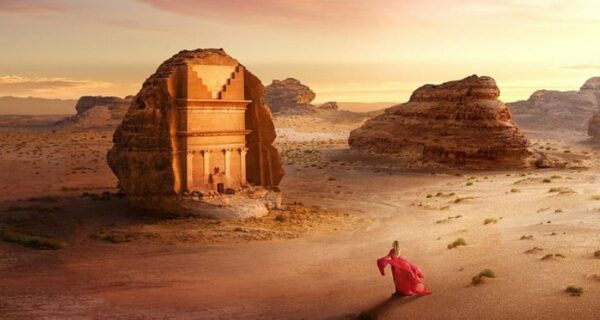
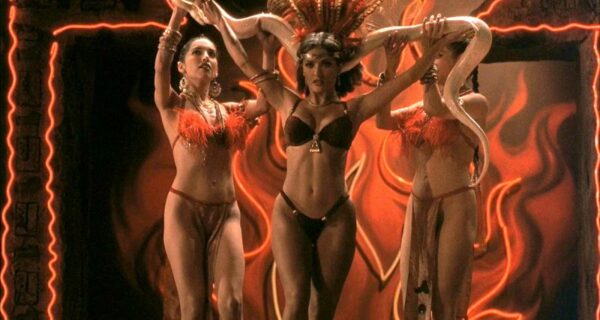
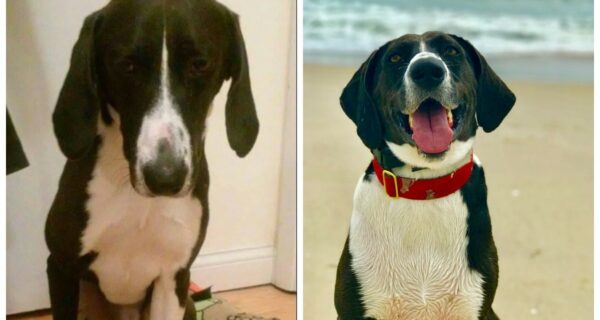
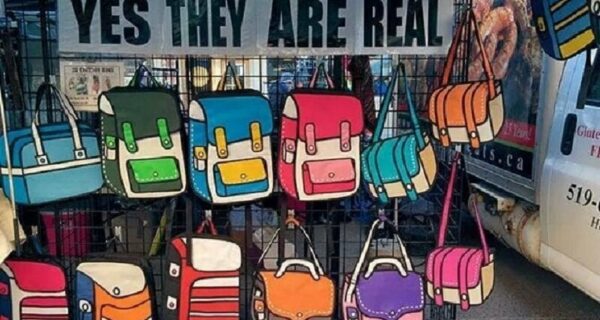